Dyneema vs. Nylon: Understanding Ultralight Backpack Materials
You’ll find Dyneema offers twice the strength of nylon at half the weight, making it ideal for ultralight builds. However, nylon excels in abrasion resistance and costs notably less—typically half the price of Dyneema fabrics. DCF provides inherent waterproofing but lacks compressibility, while nylon requires coatings but packs smaller. Your choice depends on prioritizing weight savings versus durability and budget constraints, with each material offering distinct advantages for specific backpacking applications and performance requirements.
We are supported by our audience. When you purchase through links on our site, we may earn an affiliate commission, at no extra cost for you. Learn more. Last update on 5th September 2025 / Images from Amazon Product Advertising API.
Notable Insights
- Dyneema offers twice the strength-to-weight ratio of nylon, enabling lighter pack construction without sacrificing durability or load capacity.
- Nylon provides superior abrasion resistance and longevity compared to DCF’s vulnerable laminated surface, especially at high-wear stress points.
- DCF delivers inherent waterproofing and moisture resistance, while nylon requires additional coatings and can absorb water over time.
- Dyneema materials typically cost twice as much as comparable nylon fabrics, with more limited supplier availability affecting gear options.
- Nylon compresses easily and feels softer, while DCF’s rigid laminate structure is less packable and prone to creasing.
Strength-to-Weight Performance Comparison
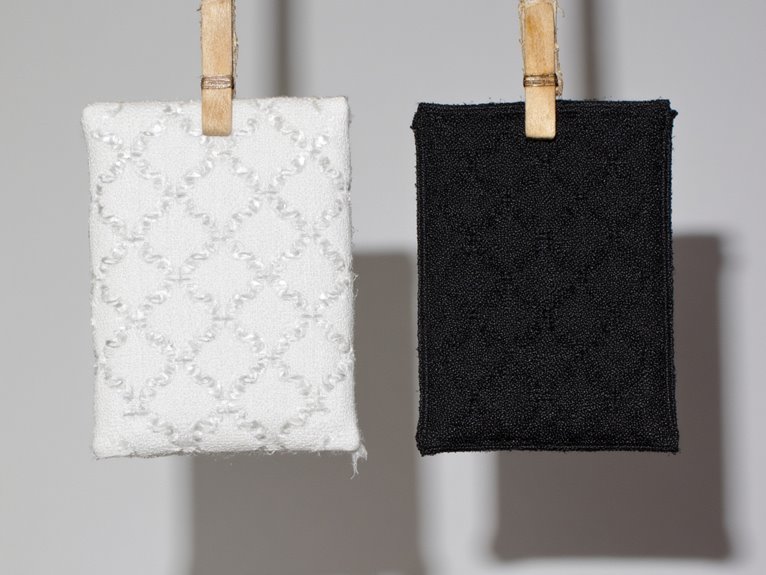
When selecting backpack materials, strength-to-weight ratio stands as the most critical performance metric for ultralight enthusiasts. Dyneema delivers unmatched performance in this category. A 100D Dyneema yarn provides roughly twice the strength of equivalent 100D nylon yarn, enabling significant weight optimization without compromising load capacity.
This advantage translates directly to pack construction. You’ll find Dyneema allows manufacturers to achieve identical strength using half the yarn denier compared to nylon. The result? Considerably lighter packs for the same carrying capacity.
Strength testing consistently demonstrates Dyneema’s superiority. Its non-woven fiber structure, laminated between Mylar layers, maximizes tensile strength while minimizing material weight.
Dyneema’s laminated non-woven construction delivers maximum tensile strength per gram, outperforming traditional materials in critical strength-to-weight testing.
Nylon’s woven construction requires more material mass to match Dyneema’s load-bearing performance, inevitably increasing your pack’s base weight.
Durability and Abrasion Resistance Analysis
While Dyneema excels in strength-to-weight metrics, its durability profile tells a different story entirely. DCF’s laminated structure places Mylar film as the outer layer, not the Dyneema fibers themselves. This creates vulnerability to surface scratching and abrasion damage that woven nylon inherently resists.
Your user experience will vary greatly between materials. Nylon’s woven structure distributes abrasion across multiple fibers, while DCF concentrates wear at stress points due to its lack of stretch. Wear patterns emerge faster on DCF backpacks, particularly at bottom corners and strap attachment points.
X-Pac consistently outperforms DCF in controlled abrasion tests. DCF’s high cost doesn’t translate to proportional durability gains. For heavily abraded applications, nylon-based fabrics deliver superior longevity per dollar spent.
Water Resistance and Weather Protection
Moving beyond durability concerns, the waterproofness gap between these materials becomes immediately apparent in wet conditions. DCF’s laminated structure provides inherent waterproofing without additional treatments.
Nylon requires waterproof coatings like TPU or silicone to achieve comparable protection.
Dyneema’s smooth surface creates superior water beading and runoff. You’ll notice water droplets roll off immediately rather than saturating the fabric face.
Nylon can “wet out” during sustained rain, though properly coated versions still prevent penetration.
For moisture management, DCF maintains pack dryness better since it doesn’t absorb water.
Nylon may retain surface moisture, slightly increasing weight during wet conditions.
However, coating degradation poses long-term concerns for nylon’s water resistance, while Dyneema maintains consistent protection throughout its lifespan.
Cost Considerations and Material Availability
Beyond weather protection capabilities, material costs create the most significant purchasing barrier between these fabrics. Dyneema typically costs twice as much as comparable nylon fabrics, reflecting its technical manufacturing process and ultra-high strength-to-weight ratio. You’ll save approximately 100 grams with Dyneema on a 30-liter pack, but price sensitivity often dictates material choice.
Material | Cost Factor | Availability |
---|---|---|
Dyneema DCF | 2x premium | Limited suppliers |
X-Pac Nylon | Moderate | Widely available |
Standard Nylon | Budget-friendly | Global sourcing |
Nylon’s cost benefits include widespread availability and established supply chains. Dyneema faces sourcing challenges with longer lead times and higher minimum orders. These availability differences affect retail pricing and production schedules, influencing your gear options and purchase decisions. Similar to ultralight sleeping bags that prioritize weight reduction under 2 pounds, backpack material selection involves balancing performance benefits against cost premiums and manufacturing complexity.
Packability and Handling Characteristics
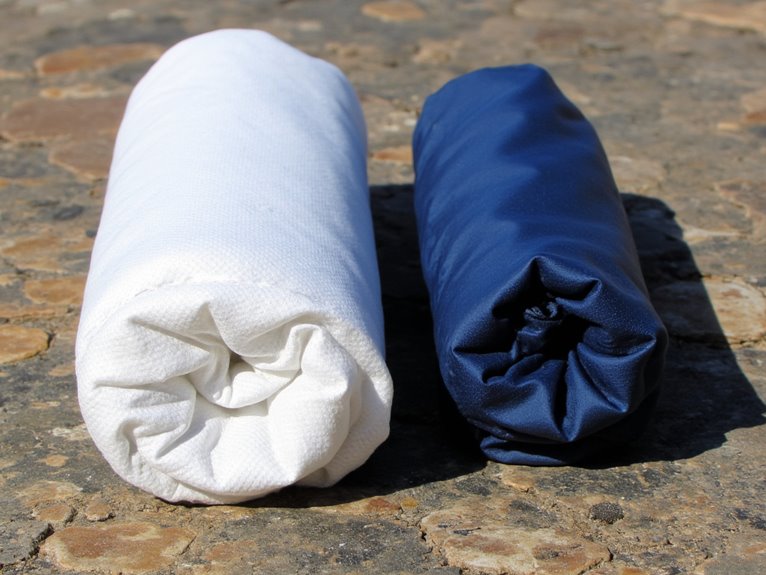
Since packability determines how efficiently your gear stows and deploys in the field, understanding the compression and handling differences between Dyneema and nylon becomes essential for ultralight backpacking decisions.
DCF’s laminate structure creates a stiffer fabric that’s less compressible than nylon variants like silnylon. You’ll need refined packing techniques to minimize wrinkles and bulk when stowing DCF gear.
Nylon compresses more easily due to its inherent fiber flexibility, yielding superior packed volume despite weighing more.
DCF feels distinctly crisp and plastic-like compared to nylon’s softer hand. This rigidity causes noticeable creasing after compression but maintains structural integrity.
Nylon’s stretch characteristics reduce seam stress under load while offering more forgiving manipulation.
Your user preferences matter greatly—some backpackers prioritize DCF’s weight savings despite handling trade-offs, while others prefer nylon’s pliability and compression advantages.
Material Construction and Industry Applications
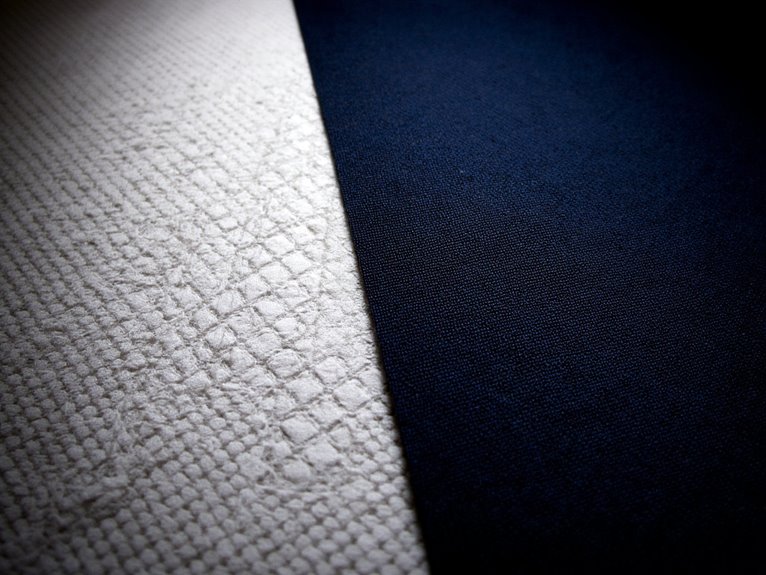
The fundamental architecture of these materials reveals why they perform so differently in backpacking applications.
DCF’s laminated construction uses ultra-high-molecular-weight polyethylene fibers in a crisscross pattern between polyester films, creating exceptional tear resistance at 2.92-5.0 oz/yd².
DCF’s innovative laminated structure achieves superior tear resistance through ultra-high-molecular-weight polyethylene fibers positioned between protective polyester film layers.
Nylon’s woven synthetic polymer structure offers flexibility but requires higher fabric weight to match DCF’s strength-to-weight ratio.
These fabric innovations drive current outdoor trends toward hybrid constructions:
- DCF dominates ultralight shelters – Zpacks Duplex Tent exemplifies waterproof, lightweight design
- Nylon reinforcements enhance durability – High-wear areas benefit from abrasion-resistant woven structure
- Challenge Sailcloth Ultra fabrics – New competitors offer improved longevity at similar weight points
You’ll find DCF in premium ultralight gear where weight savings matter most, while nylon remains the industry standard for durability-focused applications. Many leading ultralight tent manufacturers incorporate sil-nylon construction like the Featherstone Backbone, which demonstrates how different materials serve specific performance requirements in backpacking shelters.
Frequently Asked Questions
Can I Repair Tears in Dyneema and Nylon Backpacks in the Field?
You can perform field repairs on both materials using specific tear techniques.
Dyneema requires specialized adhesive patches designed for composite fabrics, applied to clean surfaces with rounded edges for proper adhesion.
Nylon accepts more versatile repair methods including fabric tape, sewing, or generic patches.
Both materials enable immediate functional restoration, though Dyneema demands precision while nylon tolerates less exact techniques.
How Do Temperature Extremes Affect Dyneema Versus Nylon Fabric Performance?
Temperature extremes dramatically impact these materials’ thermal stability and performance metrics.
You’ll find Dyneema loses half its strength by 75°C and melts at 145°C, while nylon withstands heat until 250°C.
However, Dyneema gains 5-10% strength at -50°C and performs excellently to -150°C.
Nylon absorbs water and freezes, compromising cold-weather performance.
You’ll experience better heat dissipation with nylon under friction loads.
Which Material Ages Better After Years of Storage and Use?
Your durability comparisons reveal distinct aging patterns.
DCF’s superior weather resistance maintains waterproofing and structural integrity over decades, while nylon’s UV vulnerability causes significant degradation within years.
However, nylon’s flexibility and abrasion resistance handle daily wear better than DCF’s scratch-prone Mylar surface.
For long-term storage, DCF won’t degrade like nylon’s coatings and fibers do when exposed to sunlight and moisture.
Are There Environmental Concerns With Manufacturing Dyneema Versus Nylon Fabrics?
You’ll find significant environmental differences between these manufacturing processes.
Dyneema employs sustainable practices including bio-based feedstock from timber waste, 100% renewable electricity, and emits 5 metric tons less CO2 per metric ton produced.
Nylon relies on petroleum-based polymers, generates nitrous oxide emissions 300 times more potent than CO2, and creates microplastic pollution.
Dyneema’s waste reduction strategies and circular economy initiatives outperform nylon’s environmental impact.
Do Airlines Treat Dyneema and Nylon Backpacks Differently During Baggage Handling?
Airlines don’t distinguish between Dyneema and nylon backpacks in their handling procedures.
No airline policies exist that treat these materials differently during baggage processing. Both fabrics go through identical automated systems and manual handling regardless of material type.
While baggage durability varies between Dyneema and nylon—with Dyneema being stronger but more prone to visible abrasions—this doesn’t influence how staff handle your bag.
On a final note
You’ll choose between dyneema and nylon based on your specific needs. Dyneema offers superior strength-to-weight ratios and water resistance but costs considerably more. It’s ideal for ultralight pursuits where every gram matters. Nylon provides excellent durability and abrasion resistance at lower costs, making it perfect for frequent use and rough terrain. Consider your budget, weight priorities, and intended applications. Both materials deliver reliable performance when properly constructed.